Materials Used in the Manufacturing of Rubber Expansion Joints
Rubber expansion joints, critical components in piping systems for absorbing vibrations, thermal expansion, and misalignments, rely on carefully selected materials to ensure durability, flexibility, and chemical resistance. Below is a detailed breakdown of the materials commonly used in their production:
1. Primary Elastomers
The choice of rubber compound depends on the application environment:
EPDM (Ethylene Propylene Diene Monomer)
- Properties: Excellent resistance to ozone, weathering, and high temperatures (up to 150°C).
- Applications: Water systems, HVAC, and outdoor installations.
NBR (Nitrile Butadiene Rubber)
- Properties: Superior oil and fuel resistance; operates effectively between -30°C to 100°C.
- Applications: Automotive, petroleum, and hydraulic systems.
Neoprene (Chloroprene Rubber)
- Properties: Good flame resistance and moderate chemical stability.
- Applications: Industrial machinery and moderate-temperature environments.
Silicone Rubber
- Properties: Extreme temperature tolerance (-60°C to 230°C); ideal for sterile environments.
- Applications: Food processing, pharmaceuticals, and aerospace.
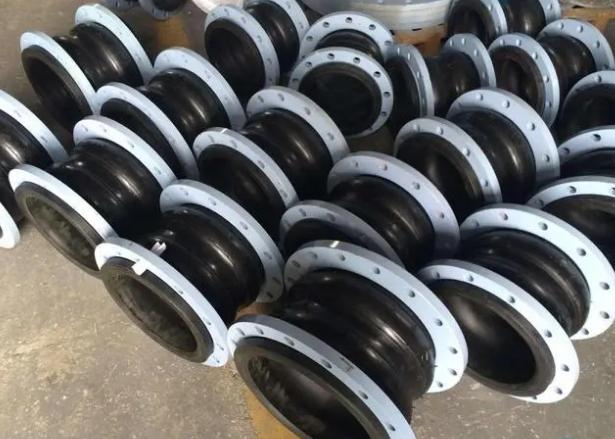
2. Reinforcement Materials
To enhance structural integrity and pressure resistance:
- Polyester or Aramid Fibers
- Provide tensile strength and prevent deformation under pressure.
- Metal Rings/Plates
- Embedded steel or stainless steel flanges for bolt connections and system integration.
- Polyester or Aramid Fibers
- Carbon Black: Improves UV resistance and mechanical strength.
- Vulcanizing Agents (e.g., Sulfur): Enable cross-linking of polymer chains for elasticity.
- Antioxidants/Antiozonants: Extend lifespan by preventing oxidation and ozone degradation.
- Inner fabric layers (e.g., nylon or polyester) reduce abrasion and improve flexibility during dynamic movements.
- Specialized bonding agents ensure seamless integration between rubber layers and reinforcement materials.
- Mixing: Raw rubber is compounded with additives.
- Molding: The mixture is shaped using compression or injection molding.
- Vulcanization: Heat and pressure cure the rubber, stabilizing its structure.
- Quality Testing: Joints undergo pressure, leak, and flexibility tests.
The performance of rubber expansion joints hinges on the synergy between elastomers, reinforcements, and additives. By selecting materials tailored to operational demands—such as temperature, chemical exposure, and mechanical stress—manufacturers ensure reliability across industries like construction, oil and gas, and water treatment.
JOINTIB has been providing cost-effective and durable rubber expansion joints and duckbill check valves . Our products are very resistant to corrosion and breakage under harsh conditions. For more information about our products, and to inquire about pricing and availability, please contact us today. You can contact us by filling out a form on our website or writing email to sales@jointib.com
Send Your Question
Recent Post
-
Has the price of rubber expansion joints in China increased?
-
Rubber Expansion Joint Manufacturing Process in China
-
Chinese Rubber Joint Manufacturer Establishes Strong Foothold in Australian Market
-
Chinese Rubber Expansion Joints Gain Popularity in the Italian Market
-
Advantages of Dual-Sphere Rubber Expansion Joints
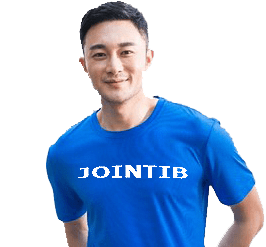
PEW
Hi, I’m the author of this post, and I have been in this field for more than 10 years. If you want to get more info about industrial pipe rubber expansion joints, feel free to ask me any questions.