Commonly Used Rubber Expansion Joint Types in the Market
Rubber expansion joints, also known as rubber flexible connectors, play a critical role in modern piping systems by compensating for movement, reducing vibration, and mitigating noise. Their flexibility, durability, and resistance to various environmental conditions make them indispensable in industries such as HVAC, water treatment, chemical processing, and power generation. This article explores the most commonly used types of rubber expansion joints in the market today, highlighting their structures, applications, and advantages.
1. Single Sphere Rubber Expansion Joint
Structure: Characterized by a single spherical rubber body reinforced with fabric or steel wire, often flanked by flanges or pipe ends for connection.
Applications: Ideal for systems requiring moderate axial, lateral, or angular movement compensation in low-to-medium pressure environments. Common in water supply pipelines, HVAC systems, and industrial pumps.
Advantages:
- Cost-effective and simple to install.
- Provides good flexibility and vibration dampening.
Limitations: Lower pressure capacity compared to multi-sphere designs.

2. Double Sphere Rubber Expansion Joint
Structure: Features two spherical rubber sections connected by a central pipe, enhancing movement absorption capabilities.
Applications: Suitable for systems with complex movement requirements, such as large-scale piping networks in power plants or chemical facilities.
Advantages:
- Accommodates greater axial, lateral, and angular movements.
- Reduces stress on adjacent equipment.
Limitations: Bulkier design and higher cost than single-sphere models.
3. Triple Sphere Rubber Expansion Joint
Structure: Incorporates three spherical rubber elements, offering maximum flexibility.
Applications: Used in high-movement scenarios, such as offshore platforms, shipbuilding, or systems exposed to extreme thermal expansion.
Advantages:
- Superior movement compensation in all directions.
- Enhanced durability under cyclic stress.
Limitations: Higher material and installation costs.
Material Considerations
Rubber expansion joints are fabricated from elastomers tailored to specific conditions:
- EPDM: Resistant to ozone, UV, and weathering.
- Nitrile (NBR): Ideal for oil and fuel resistance.
- Neoprene: Balances weather and moderate chemical resistance.
- Silicone: Suitable for extreme temperatures.
Conclusion
Selecting the right rubber expansion joint depends on factors such as pressure, temperature, movement type, and media compatibility. While single-sphere and flanged joints dominate general applications, specialized designs like PTFE-lined or triple-sphere joints address niche requirements. Regular inspection and adherence to manufacturer guidelines ensure optimal performance and longevity. As industries evolve, advancements in materials and hybrid designs continue to expand the capabilities of rubber expansion joints, solidifying their role in modern infrastructure.
JOINTIB has been providing cost-effective and durable rubber expansion joints and duckbill check valves . Our products are very resistant to corrosion and breakage under harsh conditions. For more information about our products, and to inquire about pricing and availability, please contact us today. You can contact us by filling out a form on our website or writing email to sales@jointib.com
Send Your Question
Recent Post
-
Has the price of rubber expansion joints in China increased?
-
Rubber Expansion Joint Manufacturing Process in China
-
Chinese Rubber Joint Manufacturer Establishes Strong Foothold in Australian Market
-
Chinese Rubber Expansion Joints Gain Popularity in the Italian Market
-
Advantages of Dual-Sphere Rubber Expansion Joints
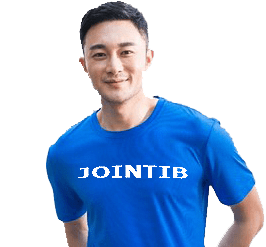
PEW
Hi, I’m the author of this post, and I have been in this field for more than 10 years. If you want to get more info about industrial pipe rubber expansion joints, feel free to ask me any questions.