Rubber VS Metal Expansion Joint, which one is best?
Both rubber expansion joints and metal expansion joints are used in a wide range of applications. They are often used to connect pumps and valves. They are often used in piping systems where there are frequent changes between hot and cold environments.
But which expansion joint is best for your specific application? Let’s take a look at the differences between these two types of expansion joint.
1. Definition
Rubber Expansion Joint is a flexible connector fabricated of natural and/or synthetic elastomers and fabric and, if necessary, internal metallic reinforcements designed to provide stress relief in piping systems due to thermal movements and mechanical vibration.
It is also called pipe rubber joints, flexible rubber joints, high pressure rubber joints, rubber shock absorbers, compensators and so on.
Metal Expansion Joint is a flexible element (bellows) constructed of relatively thin gauge material (generally stainless steel) designed to absorb mechanical and thermal movements expected in service. It is also called metal bellow.
3. Temperature
Rubber Expansion Joints with standard construction and materials have an upper range to 400°F.
Metal Expansion Joints do offer a far greater range, from -420°F to +1800°F.
4. Pressure
Rubber Expansion Joints can have pressure capabilities up to 250-psi with a full vacuum rating, which typically depending on diameter,
Metal Expansion Joints can be designed for pressures up to 1000-psi. So in high pressure applications, the strength of metal is definitely an advantage.
5. Movements
Rubber expansion joints and metal expansion joints have similar movement capabilities in the axial plane (compression and extension).
But when having similar face to face dimensions, rubber expansion joints are certainly able to absorb far greater lateral movements than metal expansion joints.
So metal expansion joints are usually used in constructions (dual or universal) where large movements in the lateral plane are required.
6. Abrasion/Erosion Resistance
Rubber expansion joints typically have a wall thickness anywhere between .0.5″ to over 1″.
Metal expansion joints on the other hand are much thinner, 012” to .080”.
The thin gauge construction of metal expansion joints makes them susceptible to erosive chemicals and abrasive liquids and slurries. So rubber expansion joints are do outperform metal joints in the applications where these conditions prevail.
7. Installation and Maintenance
Rubber expansion joints do not require additional gasketing and, in many cases, are installed easily by one or two men without the use of special handling equipment.
Metal expansion joints must be serviced occasionally to insure that the flange gasket is still intact and not deteriorated.
8. Service life
Many factors can affect the life of metal expansion joints, such as temperature, pressure, movement, vibration. So we can calculate the life of metal expansion joints through various formulas.
Rubber expansion joints on the other hand are constructed of resilient elastomers and the joint itself acts as a vibration dampener, not susceptible to fatigue/cycle failure.
Summary
Metal expansion joints are used more frequently than rubber expansion joints, mainly because the application conditions, such as temperature and pressure, favour their use.
But with its advantages, the market for rubber expansion joints is getting bigger and bigger. Rubber expansion joints can’t replace metal expansion joints in all applications, it is a better choice for many applications involving high vibration and sound dampening within the guidelines mentioned above.
It is recommended to ask us for advice on your specific application.
Send Your Question
Recent Post
-
Has the price of rubber expansion joints in China increased?
-
Rubber Expansion Joint Manufacturing Process in China
-
Chinese Rubber Joint Manufacturer Establishes Strong Foothold in Australian Market
-
Chinese Rubber Expansion Joints Gain Popularity in the Italian Market
-
Advantages of Dual-Sphere Rubber Expansion Joints
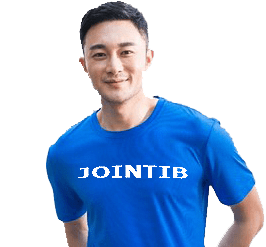
PEW
Hi, I’m the author of this post, and I have been in this field for more than 10 years. If you want to get more info about industrial pipe rubber expansion joints, feel free to ask me any questions.